In einer Zeit, in der Umweltschutz und Energieeffizienz immer mehr an Bedeutung gewinnen, stehen viele Unternehmen vor der Herausforderung, ihre Ressourcen zu schonen und gleichzeitig die steigenden Strom- und Heizkosten in den Griff zu bekommen.
Ventilatoren, die für eine saubere Arbeitsumgebung sorgen sollen, verursachen in vielen Betrieben einen bedeutenden Anteil an Stromkosten. Dabei ist der Energieverbrauch solcher Anlagen oft deutlich höher als tatsächlich erforderlich. Zudem sind veraltete Anlagen in der Regel überdimensioniert oder verfügen nicht über eine zeitgemäße Start-Stop-Automatik. Dies führt zu hohen laufenden Kosten, die keinen positiven Beitrag zur Wertschöpfung des Unternehmens leisten.
Der Gurtfördertisch von BEUTING ist schon seit 2012 bei vielen Unternehmen im Einsatz. Schon jetzt benötigt der Gurtfördertisch im Vergleich zu anderen Fördersystemen einen deutlich geringeren Volumenstrom, um einen sauberen Prozess zu gewährleisten. Durch das Absaugkonzept des Gurtfördertisches und die Nutzung eines digitalen Zwillings kann der Energieverbrauch der Anlage gezielt an die Anforderungen des Schneidprozesses angepasst und damit weiter reduziert werden. Dieser Ansatz schont nicht nur die Umwelt, sondern ermöglicht auch betriebswirtschaftlich sinnvolle Kosteneinsparungen.
Stand der Technik
Schlackewannentische
Nach heutigem Stand der Technik werden Brennschneidtische ohne Fördersystem mit Schlackewannen ausgestattet, die Kleinteile und Schlacke aus dem Schneidprozess auffangen. Je nach Maschinenauslastung und Anwendung müssen diese in regelmäßigen Abständen entleert werden, was teilweise zu einem hohen Wartungsaufwand führt. Die Schlackewannen sind über die gesamte Breite hinweg mit Löchern versehen, die den Absaugvolumenstrom gleichmäßig über die Breite verteilen. Werden kleinere Bleche verwendet, als für die Breite des Tisches vorgesehen, wird ein erheblicher Anteil an sauberer Luft abgesaugt. Ein Vorteil ist, dass das Blech an einer beliebigen Position auf dem Tisch platziert werden kann, solange ein gewisser Abdeckungsgrad der Sektion eingehalten wird. Die Effizienz der Absaugung ist somit von der Größe des Bleches abhängig, nicht aber von der Position des Bleches.
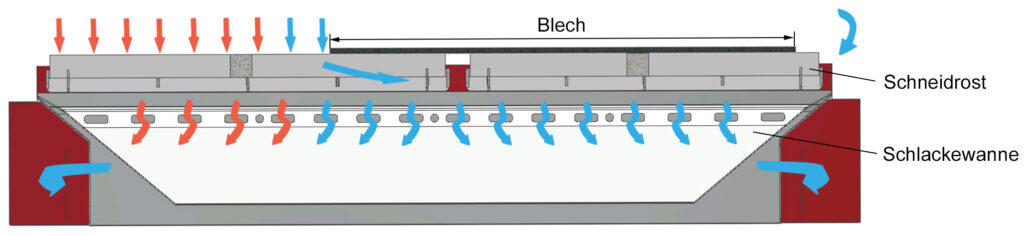
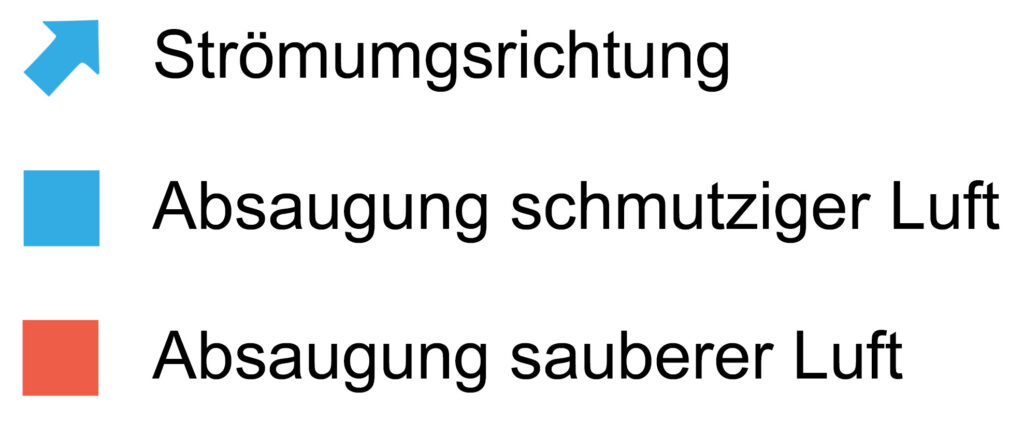
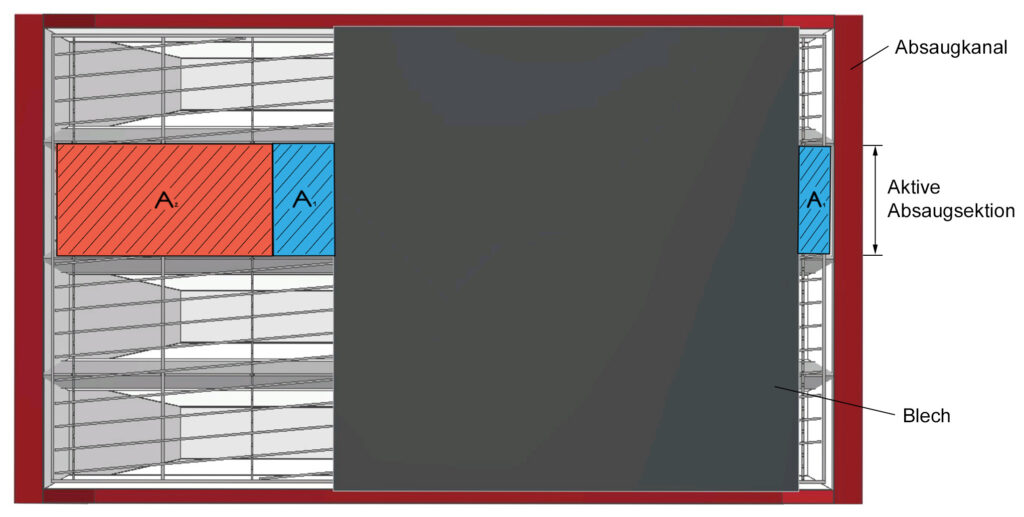
Fördertische
Die Alternative zu Schlackewannen in den Brennschneidtischen sind Fördersysteme. Der große Vorteil der Fördertische ist, dass diese die Kleinteile und Schlacke über ein Fördersystem an das Ende des Tisches befördern und die Arbeit für das Entleeren der Schlackewannen entfällt. Eine Möglichkeit zum Fördern der Kleinteile ist der Schwingförderer. Der Schwingfördertisch verfügt über u-förmige Rinnen, die das Material über Schwingungen nach und nach zum Tischende transportieren. Für diese Rinnen müssen in den Zwischenwänden Aussparungen gelassen werden. Das führt dazu, dass die Absaugsektion undicht ist und der Unterdruck für die Absaugung nur über einen hohen Volumenstrom aufgebaut werden kann.
BEUTING Gurtfördertisch
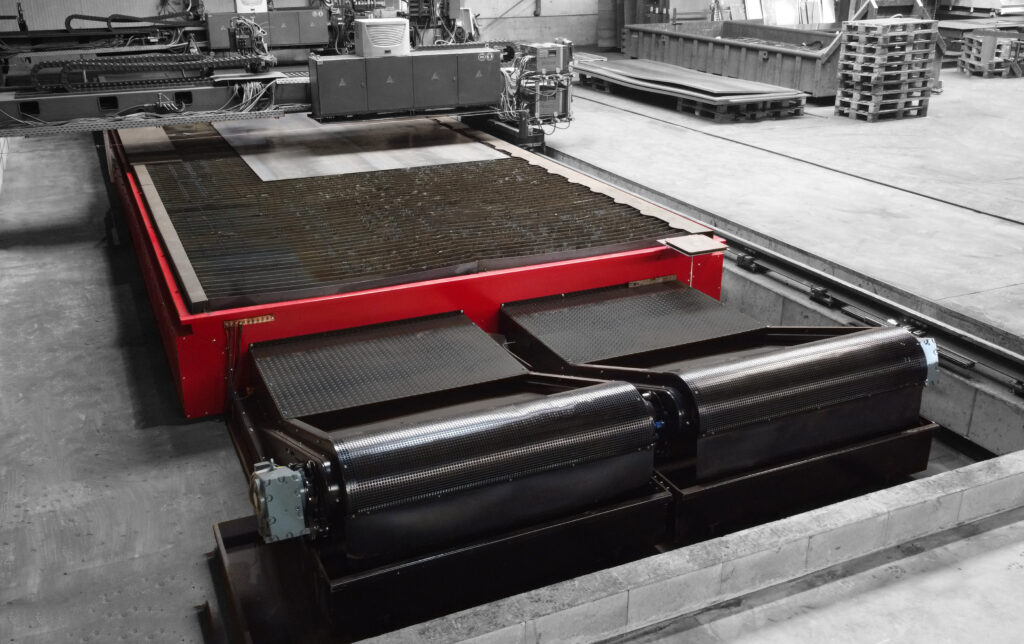
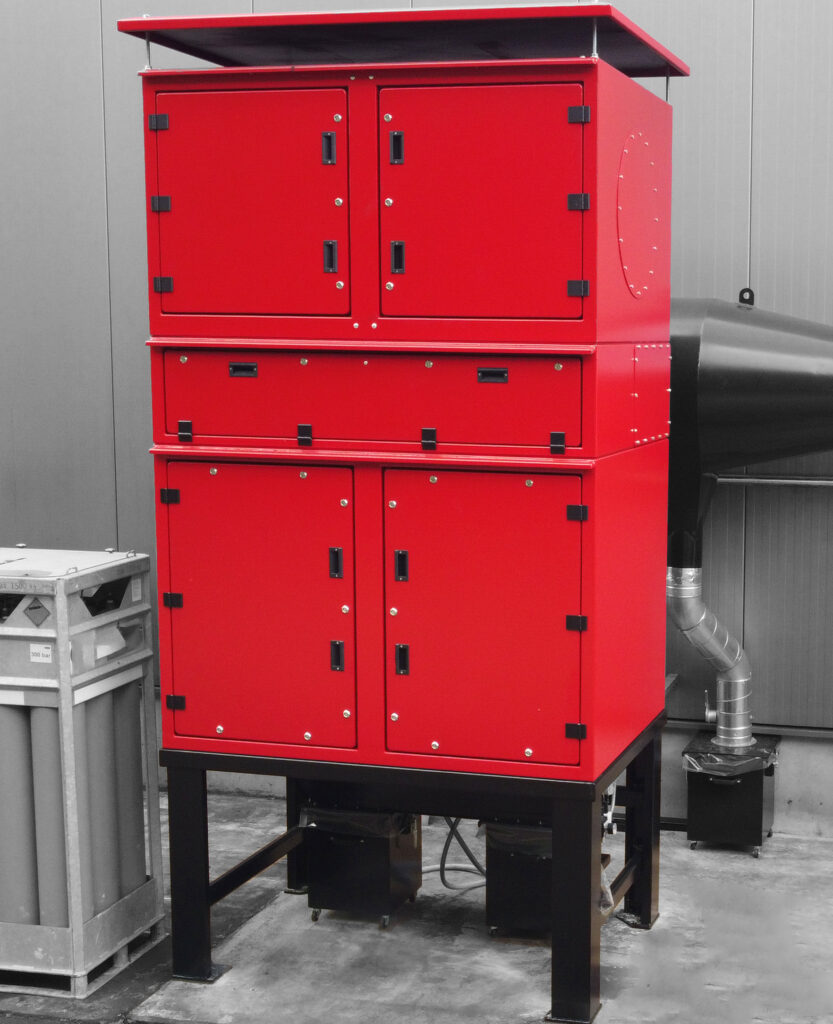
GFT500 4.600 x 13.100 mm mit Filteranlage bei BEUTING Metalltechnik im eigenen Betrieb
In 2012 wurde das Patent für den Gurtfördertisch erteilt. Kleinteile und Schlacke werden über ein Gurtförderband im Tisch aufgefangen und an das Ende des Tisches transportiert. Damit das Gurtband durch die heißen Teile nicht verbrennt, läuft es durch ein Wasserbecken. Aufgrund der Verdunstung muss das Wasser in regelmäßigen Abständen aufgefüllt werden, ein Wasserwechsel ist jedoch nicht nötig. Durch das Wasser ist die Absaugsektion nahezu 100% dicht. Im Vergleich zu anderen Fördersystemen wird daher keine Luft aus den benachbarten Sektionen angezogen.
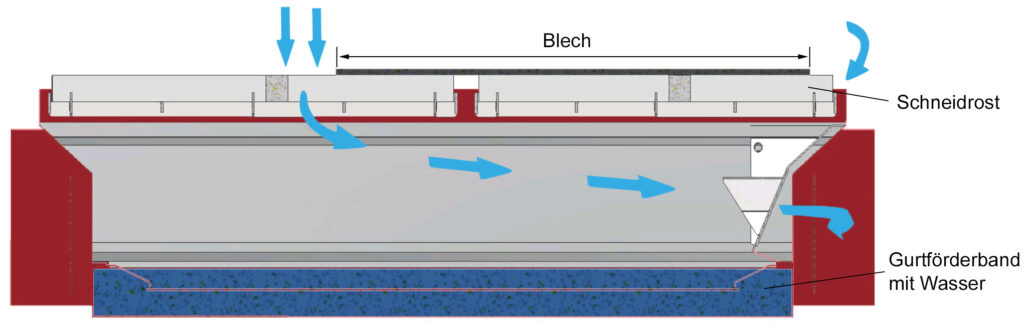
Für eine effiziente Absaugung muss das Blech nahe am Absaugkanal angelegt werden. Dadurch entsteht unter dem Blech eine Strömung, die unabhängig von der Länge des Bleches die schmutzige Luft in den Absaugkanal befördert. So können auch auf breiten Tischen ohne Probleme kleine Bleche geschnitten werden. Im Vergleich zum Schlackewannentisch, bei dem der Volumenstrom gleichmäßig über die Tischbreite verteilt ist, ist beim Gurtfördertisch das abgesaugte Luftvolumen auf die verschmutzte Luft reduziert. Für einen Großteil der Zeit ist eine minimale Absaugmenge für einen sauberen Prozess ausreichend. Durch eine intelligente Regelung können hier bis zu 90% Energie eingespart werden.
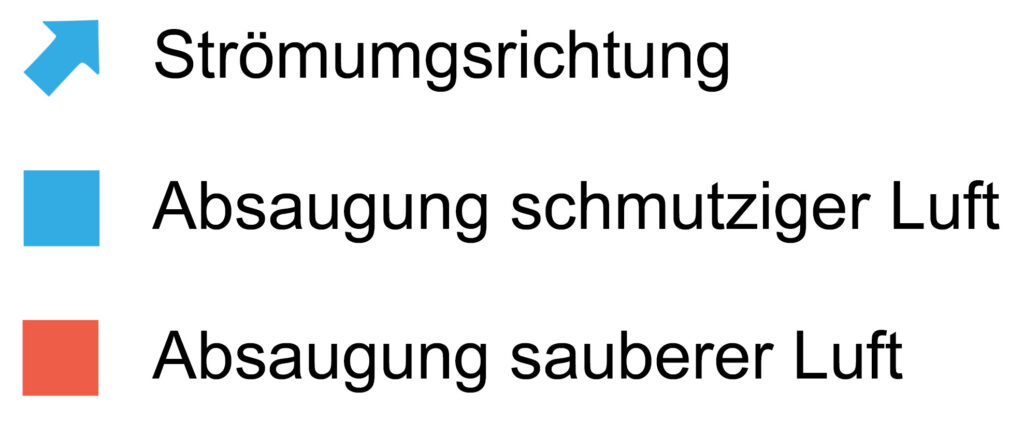
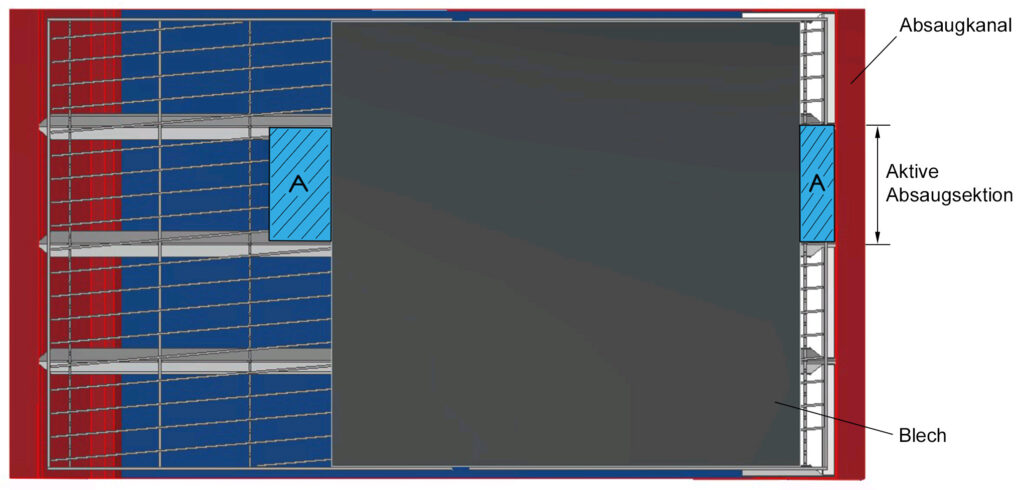
Energie sparen durch Digitalisierung
Dynamische Volumenstromregelung
Nach heutigem Standard wird die Absaugung nach dem Worst Case ausgelegt. Ohne Regelung des Ventilators bedeutet dies, dass 100% der Zeit die Luft abgesaugt wird, die für den Worst Case notwendig ist.
Was ist der Worst Case?
- Fasenschneiden. Beim Fasenschneiden wird die Luft in verschiedene Richtungen verwirbelt. Bei der Auslegung des Tisches wird ein deutlich höherer Volumenstrom für das Schneiden von Fasen vorausgesetzt. Viele Anwender besitzen zwar einen Fasenkopf, schneiden aber 80-90% der Zeit senkrecht und saugen in dieser Zeit mehr ab als nötig.
- Niedriger Abdeckungsgrad in Laufbahnrichtung. Die Sektion ist etwa 80% der Zeit in X-Richtung vollständig abgedeckt. Nur am Anfang und Ende des Bleches ist der Abdeckungsgrad teilweise unter 25%. Es sei denn der Maschinenbediener beginnt bereits während des Schneidprozesses Kleinteile abzuräumen. Für solche Situationen muss der Volumenstrom ebenfalls deutlich angehoben werden.
- Plasmaschneiden. Häufig sind Schneidmaschinen sowohl mit einem Autogen als auch mit einem Plasmaschneidkopf ausgestattet. Die Absaugung wird hierbei für das Plasmaschneiden ausgelegt. Es gibt bereits Anwendungsfälle, in denen der Volumenstrom auf das Schneidverfahren angepasst und für das Autogenschneiden entsprechend heruntergeregelt wird. Da der Autogenkopf sich jedoch häufig einen Großteil der Zeit auf der Parkposition befindet, können dadurch nur geringe Mengen an Energie gespart werden.
Die Kombination dieser drei Fälle stellt den Worst Case dar. In den meisten Anwendungsfällen sind dies nur etwa 4% der Zeit, in denen die volle Ventilatorleistung wirklich benötigt wird. In der Regel kann die Leistung etwa 64% der Zeit sogar auf ein Minimum begrenzt werden.
Digitaler Zwilling des BEUTING Gurtfördertisches
Um herauszufinden, in welcher Situation sich der Schneidprozess gerade befindet, erhält die Steuerung umfassende Informationen der Schneidmaschine. Folgende Situationen werden erkannt:
- Schneidverfahren: Plasma-, Autogen- oder Laserschneiden
- Schneidwinkel: Fasen- oder Senkrechtschneiden
- Abdeckungsgrad in Laufbahnrichtung: Vollständige oder teilweise Abdeckung
Das Absaugvolumen wird über einen Frequenzumrichter auf den Schneidprozess angepasst. Je nach Anwendung kann die Leistung einen Großteil der Zeit auf ein Minimum heruntergeregelt werden. Strom und Energieverbrauch im Vergleich zum Schwingfördertisch sinken in dieser Zeit um bis zu 90%. Die Ersparnis im Vergleich zu veralteten Schlackewannentischen ist teilweise noch höher.
Damit der Prozess stabil gehalten wird, werden weitere Messwerte verarbeitet und die Anlage ständig überwacht:
- Wasserstand im Tisch für die automatische Nachfüllung
- Volumenstrom für den ständigen Soll-Ist-Vergleich
- Füllstand der Filterpatronen für die Information über die Restlaufzeit
- Füllstand der Staubbehälter
- Stromverbrauch der Anlage für den Nachweis über die Energieersparnis
- Zustand der Gesamtanlage für eine frühzeitige Wartung
Vorteile der intelligenten Regelung auf einem Blick
1. Die Stromkosten können bis zu 90% gesenkt werden.
2. Bei den Heizkosten werden je nach Heizung etwa 50% an Energie eingespart.
3. Die CO2-Emissionen werden nachweislich verringert.
4. Der Stromverbrauch der Anlage kann ständig nachverfolgt werden.
5. Die Anlage wird während des Betriebes überwacht, wodurch ein stabiler, sauberer Prozess gewährleistet werden kann.
6. Die vorausschauende Wartung über den gesamten Lebenszyklus vermeidet ungeplante Prozessunterbrechungen.Strom